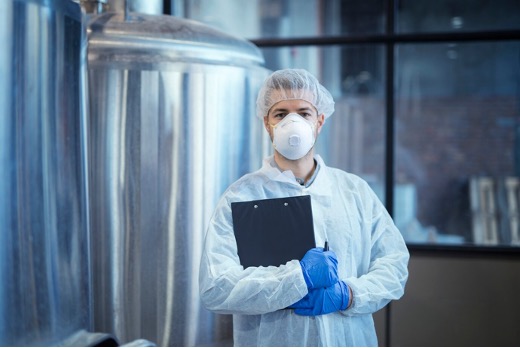
04 Dec How Quality by Design is transforming biopharmaceutical manufacturing
The biopharmaceutical industry has undergone significant transformations in recent years, particularly with the adoption of Quality by Design (QbD) principles. This innovative approach is reshaping the landscape of biopharmaceutical manufacturing by fostering a culture of quality that prioritises proactive measures over reactive solutions. This transformation not only enhances the efficiency of manufacturing processes but also ensures that patients receive safe and effective medications.
What is Quality by Design (QbD)?
Quality by Design is a strategic framework introduced to ensure that quality is built into pharmaceutical products from the outset, rather than being tested in at the end of the manufacturing process. This concept emerged from the need for a more scientific and risk-based approach to drug development, particularly in light of the complexities inherent in biopharmaceutical manufacturing.
QbD is built upon several core elements, including:
- Quality Target Product Profile (QTPP): This outlines the desired characteristics of the final product, including its intended use, dosage form, and delivery method.
- Critical Quality Attributes (CQAs): These are the physical, chemical, and biological properties that must be controlled to ensure the product meets its QTPP.
- Critical Process Parameters (CPPs): These are the variables that influence the CQAs during manufacturing and must be monitored to maintain product quality.
Understanding the process
Manufacturers are now implementing QbD principles to gain a deeper understanding of complex manufacturing processes and critical quality attributes. The approach allows companies to identify and mitigate potential risks much earlier in the development cycle, reducing the likelihood of product failures and costly interventions. It fundamentally shifts the quality paradigm from reactive testing to proactive design and control.
Regulatory agencies like the FDA have strongly endorsed QbD, creating guidelines that encourage pharmaceutical companies to adopt more sophisticated quality management strategies. The implementation of QbD provides multiple strategic advantages for biopharmaceutical manufacturers. Companies can achieve significant improvements in process efficiency, reduce production costs, and accelerate time-to-market for new pharmaceutical products. The data-driven approach allows for more precise monitoring and continuous process improvement.
Quality by Design tools and techniques
To facilitate the successful implementation of QbD, biopharmaceutical manufacturers can leverage various tools and techniques that enhance their understanding of the manufacturing process.
Risk assessment is a critical component of QbD, allowing manufacturers to identify potential hazards and evaluate their impact on product quality. By systematically analysing risks, companies can prioritise their efforts and allocate resources more effectively.
Design of experiments is a powerful statistical tool that enables manufacturers to systematically evaluate the relationships between process parameters and product quality. By conducting structured experiments, companies can identify optimal conditions for manufacturing and establish a robust design space.
Process Analytical Technology (PAT) refers to a set of tools that facilitate real-time monitoring and control of the manufacturing process. By implementing PAT, manufacturers can gain insights into process performance, enabling them to make informed decisions and maintain product quality throughout production.
How can you introduce QoD principles into your company?
Companies like Mabion provide biopharmaceutical process development services helping enterprises within the sector to comply with the principles of Quality by Design. The principles of QbD framework are built into every aspect of their manufacturing and process development services, allowing them to achieve outstanding productivity and quality of products.
Their QbD strategy is phase-specific, using a dedicated set of tools for different stages of development. The benefits of this approach include a reduced risk of failure or minimising delays during technology transfer and enhanced regulatory compliance.
As the industry continues to refine QbD principles, we can expect ongoing improvements in product quality, manufacturing efficiency, and regulatory compliance, solidifying QbD’s role as a cornerstone of modern biopharmaceutical manufacturing.
———————————————–
The information on MedicalResearch.com is provided for educational purposes only, and is in no way intended to diagnose, cure, or treat any medical or other condition.
Some links are sponsored. Products are not warranted or endorsed.
Always seek the advice of your physician or other qualified health and ask your doctor any questions you may have regarding a medical condition. In addition to all other limitations and disclaimers in this agreement, service provider and its third party providers disclaim any liability or loss in connection with the content provided on this website.
Last Updated on December 4, 2024 by Marie Benz MD FAAD